PPGI/PPGL FAQs
PPGI and PPGL have been very popular in the market in recent years due to their corrosion resistance and decorative properties. More and more people want to purchase PPGI and PPGL, but many people have many questions about these two products.
PPGI and PPGL have been very popular in the market in recent years due to their corrosion resistance and decorative properties. More and more people want to purchase PPGI and PPGL, but many people have many questions about these two products.
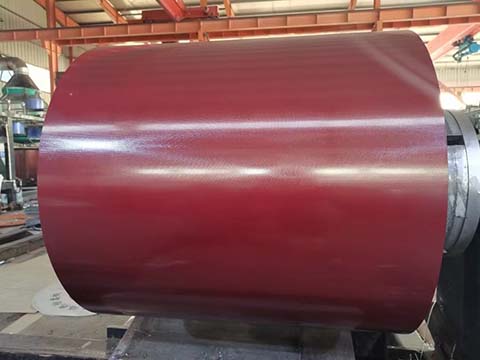
What are the full forms of PPGI and PPGL?
- PPGI’s full form is Pre-Painted Galvanized,The coating is Zinc Coating.
- PPGL’s full form is Pre-Painted Galvalume,The coating is Aluminum Zinc Alloy Coating.
What are the HS codes for PPGI and PPGL?
HS codes vary depending on the coating type, product specifications, ingredients, uses, etc. You can determine the specific HS code from the manufacturer, and the HS codes for PPGI and PPGL are under category 7210. For example:
- HS code 72107010 for painted steel with a thickness of less than 1.5mm.
- HS code 72104910 represents galvanized steel with a tensile strength of not less than 440MPa.
What types of paint coatings are there for PPGI and PPGL?
Common paint coatings for PPGI and PPGL include polyester (PE), high-durability polyester (HDP), silicon-modified polyester (SMP), polyvinylidene fluoride (PVDF), etc. Different paint coatings have different hardness, bending performance, corrosion resistance, weather resistance, etc. The following table shares the comparison of these four paint coatings:
Paint type | Hardness | Bending | Corrosion resistance | Weather resistance | Price | Film thickness (μm) |
PE | Excellent | Good | Good | Good | Low | 20 |
HDP | Good | Excellent | Great | Excellent | Medium | 20 |
SMP | Good | Good | Great | Excellent | Medium | 20 |
PVDF | Good | Excellent | Excellent | Excellent | High | 25 |
What are the grades and thicknesses of PPGI and PPGL?
- Grades: Q235 (GB), SGCC (JIS standard), Dx51d (EN standard), A653 (ASTM standard), etc.
- Thickness: 1.2-2.0mm.
Wanzhi Steel can produce the above steel grades and thicknesses. Please contact us for details.
What are the colors of PPGI and PPGL?
There are many colors for PPGI and PPGL, and Wanzhi Steel can provide all colors in all RAL color cards.
Common colors for PPGI and PPGL:
- Neutral colors: white, gray, black, beige, etc.
- Earth tones: brown, green, tan, etc.
- Bright tones: red, blue, yellow, etc.
Which one is better for roofs, PPGI or PPGL?
Both PPGI and PPGL are suitable for use on roofs. You only need to consider the application environment and cost budget.
PPGI is cheaper than PPGL, but PPGL has higher corrosion resistance than PPGI. PPGL is more suitable for harsh outdoor environments, such as coastal areas.
The following table recommends the coating weight of PPGI and PPGL in different corrosion environments:
Substrate type | Nominal coating weight (g/㎡) | ||
Corrosive environment | |||
Low | Medium | High | |
Zinc coating (Z) | 90/90 | 125/125 | 140/140 |
Aluminum-zinc coating(AZ) | 50/50 | 60/60 | 75/75 |
Note: PPGI uses Zinc coating, and PPGL uses Aluminum-zinc coating (AZ)
What is the difference between PPGI and PPGL?
The difference between PPGI and PPGL can be analyzed from the aspects of substrate, substrate composition, weight, appearance, corrosion resistance, weather resistance, service life, application and price.
Difference | PPGI | PPGL |
Substrate material | Galvanized steel (GI) | Galvalume (GL) |
Substrate composition | Mainly zinc | Aluminum-zinc alloy (usually 55% aluminum, 43.3% zinc, 1.5% silicon) |
Weight | Coating thickness is the same, Zinc coating weight is heavier | Because aluminum has a lower specific gravity than zinc, aluminum-zinc coating is lighter |
Appearance | Surface is smooth and shiny | Because of aluminum, aluminum adhesion is good, the surface is smoother and the gloss is better |
Corrosion resistance | Good corrosion resistance | Because of the combination of aluminum and zinc, the corrosion resistance is better than PPGI |
Weather resistance | Good | Better weather resistance than PPGI, can withstand temperatures up to 315℃, and can better resist wind and rain erosion |
Durability | Good | More durable than PPGI |
Application | Building wall panels, roofs, warehouses, shopping malls, cars, home appliances, etc. | Scenarios that require higher corrosion resistance |
Price | Relatively low | Relatively high, because of its better performance |
Service life | 20-30 years | PPGL has a service life of 2-3 times that of PPGI. |
Which one is better, PPGI or PPGL?
From the table above, we can see that the overall performance of ppgl is better than that of ppgi, and the price of ppgi is relatively low.
After comparing the two, each has its own advantages and disadvantages. When choosing, you should consider where you will use it? What is the cost budget of the project?
It should be noted that PPGL does not have as many colors as PPGI, and PPGL has certain limitations in using colors.
Are PPGI and PPGL fireproof?
PPGI and PPGL are not fireproof in themselves. Both have certain heat resistance. PPGL has better heat resistance and can withstand temperatures up to 315℃.
How to calculate the weight of PPGI and PPGL?
Before calculating the weight of PPGI and PPGL plates, we must first understand their density. The density of PPGI and PPGL plates is 7.85g/cm³. Secondly, we must understand the weight calculation formula. The calculation formulas for both are the same.
Calculation formula: Weight (KG) = length (m) * width (m) * thickness (mm) * density
For example: a PPGI steel sheet with a length of 1500mm, a width of 900mm, and a thickness of 0.5mm.
Weight = 1.5*0.9*0.5*7.85=5.29875kg
What is the ISO standard GSM for PPGI steel sheets?
In the standard system for galvanized steel sheets and related materials, GSM (Grams per Square Meter) is usually used to describe the weight of the zinc coating, that is, the weight of the zinc layer per square meter of steel sheet, which is an important indicator for measuring the corrosion resistance of galvanized steel sheets.
How to deal with GI and GL before painting
In order to ensure the adhesion and corrosion resistance of the coating, GI and GL substrates need to undergo a series of treatments before painting.
- Degreasing: To remove oil, grease and other impurities on the surface of the steel.
- Water washing: Used to remove residues on the surface of the steel, such as degreasing agents, pickling solutions, etc.
- Phosphating: A relatively important step. In order to enhance the corrosion resistance of the coating, the steel plate is immersed in a solution containing phosphates. A stable phosphate film is formed on the surface of the steel through chemical reactions, which can improve the adhesion of the coating.
- Passivation: The passivation treatment is to further improve the corrosion resistance of the phosphate film.
- Drying: Dry the steel plate to remove moisture from the surface.
- Inspection: Perform a comprehensive inspection of the steel plate to ensure that there are no defects such as oil, rust, scratches, etc. on the surface.
What are the advantages of PPGI and PPGL produced by Wanzhi?
- Production: 3 pre-painting production lines to ensure product delivery; more than 200 rollers to produce various patterns.
- Inspection: Complete testing process to ensure product quality, including thickness test, coating/paint thickness test, gloss test, salt spray speed test, impact test, weather resistance test, etc.
- Packaging: Wanzhi Steel ensures that all packaging is very strict and meets the required standards to avoid damage during transportation and storage.
- Experience and Service: We have 13 years of experience in steel export, and our products have been exported to more than 120 countries. We have successfully completed more than 1,200 foreign projects and received praise from customers from different countries.
Product Category
Coated Steel
- GALVANIZED STEEL COIL
- GALVALUME STEEL
- HOT DIP GALVANIZED STEEL
- ELECTRO GALVANIZED STEEL
- GALVANIZED CORRUGATED ROOF SHEET
- ZAM STEEL
Color coated steel
- PPGI STEEL COIL
- CORRUGATED STEEL SHEETS
- PPGL
- PATTERN PPGI
- PREPAINTED STEEL SHEETS
- PPGI FOR WRITING BOARDS
- PPGI FOR FENCE
- PPGI FOR HOME APPLIANCES
- PREPAINTED ALUMINUM COIL
- MATT TEXTURED PPGI
- COLOUR COATED ROOFING SHEET
Roofing Sheet
Stainless Steel
Other Coil & Sheet
- COLD ROLLED COILS
- HOT ROLLED STEEL
- EMBOSSED STEEL
- METAL CARVED PANEL
- COLD ROLLED STEEL SHEET
- PERFORATED SHEET METAL
- Q235 STEEL
CONTACT US
- Mobile: +8617637100809
- Whatsapp: +8615138685087
- Email: info02@wanzhisteel.com
- Address: 10F, Building B, Erqi Center, Erqi District, Zhengzhou City, Henan Province, China