Hot-dip galvanized steel, with excellent anti-corrosion properties, and the emergence of hot-dip galvanizing technology have greatly extended the service life of steel. Whether for construction, bridges, ships, power, communication, or transportation, especially where high anti-corrosion performance is required, such as marine engineering, chemical equipment, and other fields, hot-dip galvanized steel has always been the material of choice.
The hot-dip galvanizing process improves the adhesion and uniformity of the zinc layer and reduces the cost, making it increasingly competitive. This article takes you through the many facets of galvanized steel. It includes its uses, benefits, properties, definitions, whether it is rustproof, process, and coating.
What is hot-dip galvanized steel
What does hot-dip galvanizing mean?
Galvanizing is a method of preventing rust by coating the surface of steel with metallic zinc. Hot-dip galvanizing is a method of galvanizing that consists of three parts: pre-treatment, hot-dip galvanizing, and post-treatment. It is an effective method of metal corrosion prevention. It dips the descaled steel parts into the molten zinc liquid at about 500℃, so that a zinc layer is attached to the surface of the steel parts to achieve the purpose of anti-corrosion. Hot-dip galvanizing has the advantages of uniform coating, strong adhesion and long service life.
-Suburban environments: Standard hot-dip galvanizing rustproof thickness lasts for more than 30 years without maintenance.
-Urban or offshore areas: Standard hot-dip galvanized rust-proof thickness lasts for 20 years without repair.
What is hot-dip galvanized steel made of?
As the name suggests, it is steel and belongs to steel. Hot-dip galvanized steel is made by continuous hot-dip plating of hot-rolled steel strip and cold-rolled steel strip.
Can aluminum be hot-dip galvanized? What other materials are available?
Yes, it can be hot-dip galvanized. Aluminum that has been galvanized is hot-dip galvanized aluminum. However, pure aluminum is not suitable for hot-dip galvanizing, but aluminum alloys can be hot-dip galvanized under certain conditions. Materials that can be galvanized in daily life include iron, steel, aluminum, and copper. Iron and steel are common galvanizing materials with ideal galvanizing results. Other materials are recommended to use other rust prevention methods.
In summary, iron, steel, and copper can be galvanized by appropriate pretreatment, and aluminum can be galvanized by special treatment.
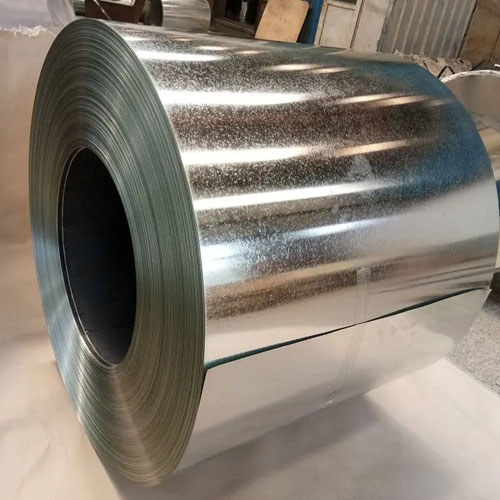
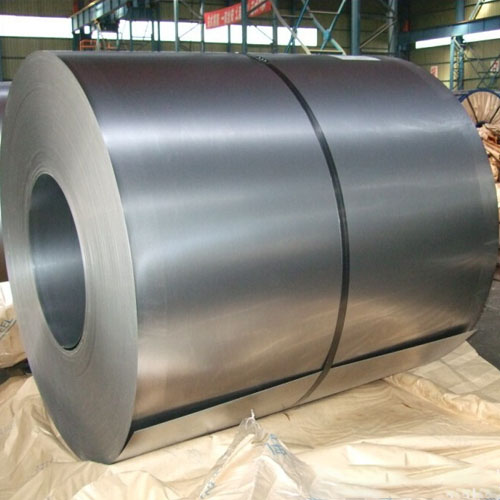
What are the properties of hot-dip galvanized steel?
Hot-dip galvanized steel plays an important role in many fields with its excellent anti-corrosion properties, decorative properties, processing properties, and electrical conductivity. It is widely used in construction, home appliances, automobile, machinery, electronics and other industries. The following are its main characteristics:
- Tensile strength, yield point, elongation are in line with the standard
- Corrosion resistance and durability, can be used for decades
- Beautiful and bright, highly decorative
- High hardness and strength, compression and tensile resistance
- Anti-vibration, anti-impact, windproof
- Good electrical conductivity
- Easy to process, can be made into various shapes
- Affordable and readily available
- No harmful chemicals used in the production process, no pollution to the environment. Long service life and recyclable.
These are the advantages of hot-dip galvanized steel sheet. Although hot-dip galvanized steel sheet has many advantages, you must also pay attention to maintenance and choose the right specifications according to the specific requirements.
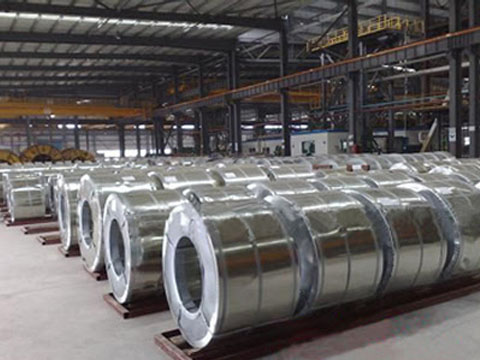
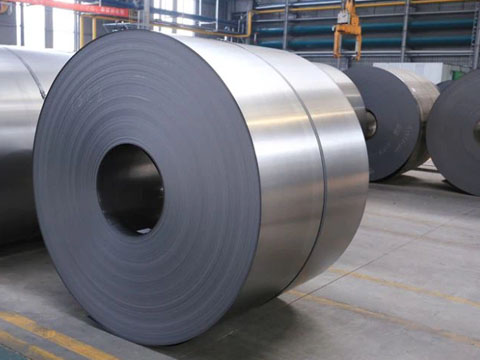
What is hot-dip galvanized steel used for?
- Construction
Steel buildings, train stations, aerospace facilities, roofs, walls, tops and fittings, skeletons. - Agriculture
Hot-dip galvanizing can better prevent corrosion problems in large-scale agricultural machinery, corrals and pens. - Electric power and communication industry
Wire poles, utility poles, transformer shells. In the communication industry, cabinets, brackets and antenna poles for communication equipment. - Transportation field
Highway guardrails, bridges, ships, etc. These facilities have to withstand harsh environments - Automobile industry
Automobile interior and exterior panels, frames, fuel tanks, chassis and other parts manufacturing - Home appliances and light industry
Refrigerator, washing machine cooler, air conditioning and other equipment, light industry, furniture, warehouses, supermarket shelves, billboards and so on.
What is the difference between pre-galvanized steel and hot-dip galvanized steel?
There are some differences between the two in terms of process, effect, application, etc., as follows:
- Difference in process
Pre-galvanized steel is galvanized before steel processing. After processing, there is no zinc layer to protect the holes, cut surfaces and sections, and the sections are prone to corrosion and rust. Hot-dip galvanized steel is made by dipping steel into a molten zinc pool. Through chemical reaction, the coating is firmly attached to the steel surface. - The difference between the thickness of the coating and the anti-corrosion effect
The galvanized layer of pre-galvanized steel is generally 5μm, compared with the thicker layer of hot-dip galvanized steel, which is usually 45~85μm. Therefore, hot-dip galvanized steel has better anti-corrosion effect. - Difference in application areas
Hot-dip galvanized steel is used in electric power towers, communication towers, railroads, street light poles, ship components, substation ancillary facilities and light industry. Although pre-galvanized steel also has some anti-corrosion effect, its application range may be narrower.
How to galvanize hot dip galvanizing?
The galvanizing process of hot-dip galvanizing consists of three main parts: pre-treatment, hot-dip galvanizing and post-treatment.
- Preprocessing
Including degreasing (if necessary), pickling, weight reduction, water washing, plating aid, drying, etc. Degreasing removes surface oil and pickling removes surface oxides and rust. Cleaning with water removes residual acids and detergents from the surface and helps form a thin film on the surface for the zinc solution to adhere to. Dry to remove excess moisture on the surface to avoid zinc explosion and missing plating. - Hot dip galvanizing
The dried workpiece is immersed in molten zinc for galvanizing. During the galvanizing process, the zinc liquid temperature, workpiece lifting speed, angle, etc. are all intelligently controlled by the program. - Post-processing
Including water cooling, passivation, inspection and packaging, storage. Water cooling is to lift the component and quickly turn the liquid zinc on the surface into solid crystal zinc through air cooling or water cooling before the coating turns gray. Passivation prevents the formation of white rust. Inspection and packaging is when workers inspect the surface of the plated parts to ensure that there are no leaks, zinc nodules, zinc thorns, color differences, etc., and then check the thickness of the zinc layer, and put the qualified plated parts into storage.
In general, the hot-dip galvanizing process is a complex and delicate process, and the process parameters of each step need to be strictly controlled to ensure the quality and effect of galvanizing.
What is the difference between hot dip galvanizing and spray painting?
The surface treatment methods of hot-dip galvanizing and spray painting are different, so the effects are different in many aspects.
- Service life
In general environment, hot-dip galvanizing has excellent anti-corrosion performance and can keep rust-free for about 30 years. Spray painting can generally only be used for 3-5 years. In areas with large climate changes, it can only be used for 1-2 years. - Construction difficulty
Hot-dip galvanizing can be installed and operated directly on site without additional protective measures and is simple to construct. Spray painting is affected by many factors such as the operator’s technical proficiency, paint viscosity, working air pressure, distance between the spray gun and the object, and is also affected by weather, so the construction is difficult. - Appearance
The zinc layer of hot-dip galvanizing has good covering ability, dense coating, no organic inclusions, and high appearance quality. The corrosion resistance of spray paint is not ideal and it is easy to peel off, affecting the appearance. - Principle
Hot-dip galvanizing is the reaction of molten metal with an iron matrix to form an alloy layer. The substrate and coating are tightly combined, and the zinc layer is strong and corrosion-resistant. Spraying uses a spray gun and a disc atomizer to disperse the paint into uniform and fine droplets, which are applied to the surface of the object to be coated and baked at high temperature to form.
To sum up, there are obvious differences between hot-dip galvanizing and spray painting in terms of principle, anti-corrosion life, construction convenience, appearance, etc. There are specific considerations to consider when choosing which method to use.
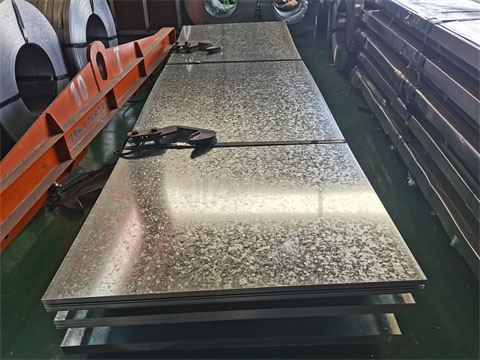
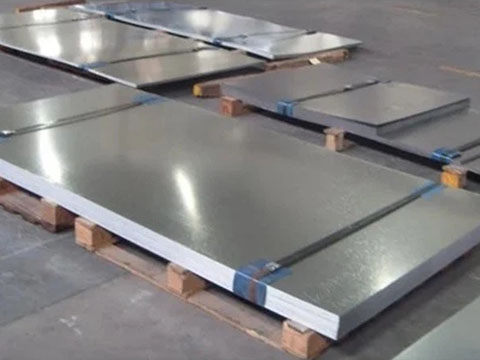
How thick is hot dip galvanizing?
The thickness standard of hot-dip galvanizing is related to the thickness of the plated parts.
Thickness of plated parts | Hot-dip galvanizing average thickness | Hot-dip galvanizing local thickness |
≥6mm | >85μm | >70μm |
3-6mm | >70μm | >55μm |
1.5-3mm | >55μm | >45μm |
According to the national standard《GB/T 13912-2002 Technical Requirements for Metal Covering and Steel Coatings》, the thickness of the galvanized layer of hot-dip galvanized steel pipes must be above 35 μm. In practical applications, the thickness of hot-dip galvanizing steel products is generally above 45 μm, and can even reach 200 μm.
Note that the thickness of hot-dip galvanizing is not as thick as possible. An excessively thick zinc layer may affect its service life.
FAQ about Hot-Dip Galvanized Steel
What is the service life of hot-dip galvanized steel?
Hot-dip galvanized steel can last 20 to 30 years without rusting. The specific service life is related to the actual environment, zinc layer thickness, use, zinc layer quality, etc.
Can hot-dip galvanized steel prevent rust?
Hot-dip galvanizing provides protection against rust. Hot-dip galvanizing is a process in which the surface of steel is immersed in molten zinc to form a zinc layer with a thickness of 10 to 25um. This zinc layer prevents steel from corroding and acts as a good rust inhibitor. If the zinc layer is damaged, it can cause the steel to rust. So pay attention to maintenance.
Are there any other methods of galvanizing?
There is also electro-galvanizing, also called cold galvanizing, which does not require high-temperature treatment. After pretreatment, electrolysis is mainly used. The electroplated part serves as the cathode and the zinc solution serves as the anode. After energization, the zinc ions in the galvanizing solution move toward the cathode under the action of potential difference, forming a uniform zinc layer.
Can hot-dip galvanized steel be welded?
The answer is yes. It can be welded. Generally, electric welding or gas shielded welding can be used for thinner zinc layers, and argon arc welding with electrodes is recommended for thicker zinc layers. Gas shielded welding is mainly used for welding that is inconvenient to grind and has a zinc layer.
Can Hot-dip Galvanized Steel be Colored?
Hot-dip galvanized steel can be colored. It is coated by roller coating, then cured at high temperature and cooled to make pre-painted galvanized steel. There are many colors and types (PE, SMP, HDP, PVDF) of organic coatings to choose from.
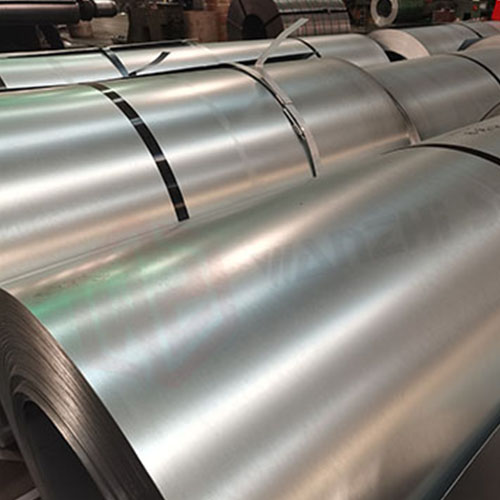
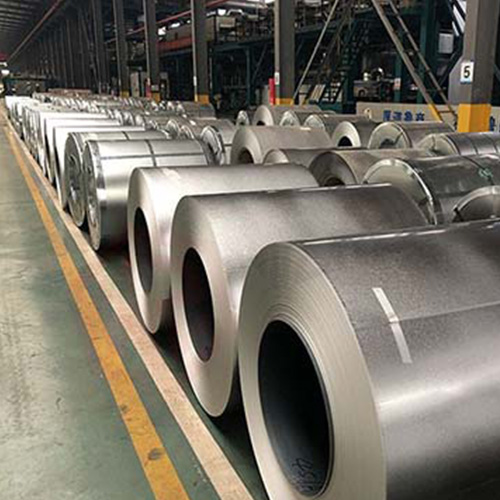
What Galvanizing Process Is Used At WanZhi?
Galvanizing is a popular manufacturing method, mainly divided into hot dip galvanizing and cold galvanizing, cold galvanizing is also called electro galvanizing, electro galvanizing is also divided into acid plating and alkalinity.
Wanzhi Steel Group adopts hot-dip galvanizing and electro-galvanizing processes, and has two hot-dip galvanizing production lines and one electro-galvanizing production line.
Conclusion
Hot Dipped Galvanized Steel involves placing iron into molten zinc, which causes a layer of zinc to adhere to the surface of the plated part. It is used to protect 80% of the world’s manufacturing industry against rust. Galvanization optimizes the performance of the plated parts and greatly improves the durability of GI steel products, and the Hot Dipped Galvanisation process is the most commonly used method of galvanization.
If you have a project in hand that requires this material, come and visit our production line, galvanized coils and sheets for sale!